Archives
Contribute
|
Technology - Electrospun Polycarbonate Nanofibers
|
|
Nirupama Kattamuri 05/16/2004
(This article is sponsored by The Boston Group)
INTRODUCTION
In contrast to conventional spinning methods like melt spinning, dry spinning etc, electrospinning is an emerging technology, which can produce fibers in the sub-micron to nanorange. The high surface area to volume ratio and the high porosity values makes the fibers advantageous in various applications like manufacture of filtration membranes, nanotubes, protective clothing and the like. The process involves in dissolving a suitable polymer in a solvent to form a viscous solution. In our case polycarbonate of Bisphenol A was chosen as it is thermoplastic and can be made flexible at higher temperatures. The dissolved solution was then taken in a syringe and pumped to the tip of the needle with the help of a flow meter. With the application of a critical voltage to the solution the polymer undergoes a whipping process. The surface tension of the solution is overcome by the electric potential and the polymer starts spinning. During the spinning process the polymer bends and stretches to form fibers. The solvent evaporates during the travel of the fibers towards the grounded target to get a fresh dried mat of electrospun fibers collected on the aluminium foil.
EXPERIMENTAL CONDITIONS
The polycarbonate of Bisphenol A of MW 27,000 Daltons and two solvents THF and DMF were purchased from Aldrich Chemical Company Inc. and used without any further processing. The design of experiment was first performed and then electrospinning was done at concentrations ranging from 14 to 18%, voltage 25-30 kV, flow rate 0.01 to 0.5 ml/min and distance 4.5 to 10 inches. A solvent mixture ratio of THF: DMF = 60:40 was used. The temperature and humidity were monitored throughout the experiment. The spun fibers were then imaged with an AMRAY 1400 scanning electron microscope and Philips EM 400 T transmission electron microscope. The image processing to measure the bead density and fiber thickness was done with the help of image processing softwares like GAIA Blue and Scion Imaging.
RESULTS AND DISCUSSION
Effect of polymer concentration
Electrospinning was performed for polymer concentrations varying from 14% to 18% polycarbonate solution. It was found that as the concentration increased the fiber thickness increased. This is because of the increase in the viscosity of the solution, which made it difficult for the polymer to stretch into fibers. As a result, thicker fibers were formed at 18% concentration solution than those at 14% concentration solution. It can be seen from the SEM images in Figure 1 that the fiber thickness increases with concentration.
However there was a decrease in the bead density from 29.15% at 14% concentration to 9.26% at 18% concentration. Beads are nothing but irregular shapes of fibers formed due to poor processing conditions. The surface tension of the polymer is the main cause for the formation of beads. With increase of concentration, the viscosity overcomes the surface tension thereby decreasing the bead formation.
Effect of flow rate
The rate at which the polymer was being ejected from the tip of the syringe was well controlled to see its effect on fiber formation. It was found that flow rate had a profound effect on the fiber thickness and bead density. Thinner fibers were obtained at lower flow rates than at higher ones. Fibers obtained at a flow rate of 0.1 ml/min were 30-40 nm thicker than those obtained from 0.01 ml/min. Thus a lower flow rate was preferable. However at very high flow rates like 0.5 ml/min fibers were not formed because the polymer did not have enough time to spin. Blobs of polymer were sprayed onto the target instead of fibers. This process is termed as electrospraying and not electrospinning. So, an approximation had to be found between these two values in order to generate fine fibers.
The bead density was also found to decrease with flow rate.
Figure 1. Effect of concentration on fiber thickness. DESIGN OF EXPERIMENT (DOE)
The design of experiment was conducted to find the most significant parameter from all the processing parameters to reach the goals of generation of uniform beadless nanofibers. With the help of Minitab software a set of experimental conditions were obtained. After measurement of the fiber thickness and bead density, values were entered into the software. Then the software analyzed the data and produced Pareto charts, which showed the most significant factor for our responses.
EFFECT OF DISTANCE
It was found that distance had a major effect on the fiber formation. In the present work electrospinning was done for distances varying from 4.5 to 10 inches, flow rate from 0.05 to 0.1 ml/min by maintaining a polycarbonate concentration of 16%, voltage of 30 kV. It was found that fibers formed at 10 inches were more uniform and negligible in bead density values than those spun from 6 and 8 inches. This can be explained because the spinning for 6 and 8 inches was done during the winter when the temperatures and humidity were low. But when the spinning was performed for 10 inches, it was summer and the temperatures and humidity had risen considerably. But uniform fibers were attained as seen from Figure 2. Since all other parameters were maintained constant, humidity and temperature are concluded to have a major role in polycarbonate electrospinning.
CONCLUSIONS
We were able to produce uniform, smooth polycarbonate nanofibers with minimum bead densities at a concentration of 16% polycarbonate, flow rate of 0.01 ml/min, voltage of 30 kV, distance of 10 inches, solvent mixture ratio of THF: DMF = 60:40. Also from DOE analysis Pareto chart it was found that concentration is the most significant parameter for fiber thickness and bead density to obtain uniform nanofibers of 150-200 nm fiber thickness.
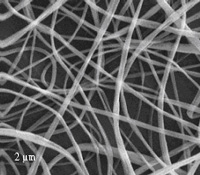
Figure 2. Uniform Polycarbonate nanofibers. (Nirupama Kattamuri received her M.S. from the Department of Chemical and Nuclear Engineering,
University of Massachusetts, Lowell and currently works at VICR Corp. She was a recepient of an award for her poster at the International Metallographic Society.
)
|
You may also access this article through our web-site http://www.lokvani.com/
|
|